It has high strength, which is one of the advantages of die-casting aluminum parts. When we choose a die-casting alloy, we must fully consider the function and occasion of use. Its performance characteristics are excellent and it is widely used. I believe that many friends do not know about the process steps of die-casting aluminum parts. I know very well, so let me give you a brief introduction.
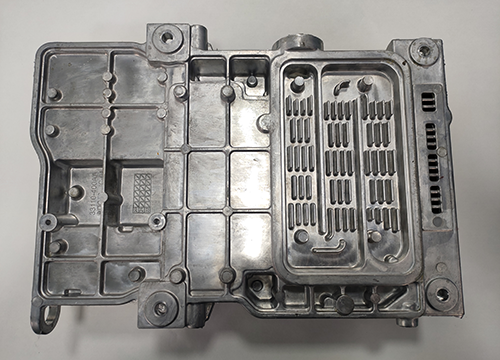
The die casting process of new energy vehicle die castings mainly consists of four steps, or is called high pressure die casting. These four steps, including mold preparation, filling, injection, and shakeout, are also the basis for various modified die casting processes. Lubricant is sprayed into the mold cavity during the preparation process. In addition to helping to control the temperature of the mold, the lubricant can also help the casting release. The mold can then be closed and the molten metal injected into the mold at high pressure, which ranges from about 10 to 175 MPa. After the molten metal is filled, the pressure is maintained until the casting solidifies. The push rod then pushes out all the castings, and since there may be multiple cavities in a mold, there may be
Die Casting Robot Parts multiple castings per casting.
Die-casting aluminum parts have good casting performance, high dimensional accuracy, stable performance, and can be recycled, saving production costs, so they have a wide range of applications.
At present, the aluminum alloy die-casting process has been widely used in various fields. The aluminum alloy die-casting products are currently mainly used in auto parts, electronic shells, communications, motors, aviation, ships, home appliances, furniture accessories, digital shells, handicrafts, Security product shells, LED lighting (lampshades) and some new energy industries, etc., some high-performance, high-precision, high-toughness high-quality aluminum alloy die-casting products are also used in large aircraft, ships and other industries with relatively high requirements. The main use is still on the parts or shells of some instruments, because the aluminum alloy forming process has become a widely used process.
One of the ways of aluminum casting for aluminum alloy die casting process is die casting. Die-casting steel molds, or dies, are joined by injection of molten metal under high pressure. The wide application of aluminum alloy die-casting technology, the die-casting process may be the commonly used casting process, compared with other aluminum casting processes. The die-casting method is an application suitable for the production of small to medium-sized parts that require large quantities of parts. The parts produced by die-casting are more detailed, bringing more exquisite surface quality and dimensional consistency.
Aluminum casting processes are used for lawnmower housings, street light housings, typewriter frames, dental appliances, frying pans, cover plates, exterior containers, escalator parts, conveyor parts, aircraft and marine hardware and lighting rings and Produced aluminum alloy outboard motor parts.
Aluminum alloy die-casting in four steps. First, the oil is applied to the mold, and then the mold is closed. The oil will help control the temperature of the mold and it will make casting removal easier. Then, the molten metal will be forced into the mold under high pressure. The high-pressure eruption requires rapid filling of the mold before the casting hardens. The mold will be replenished and pressure will be maintained until the molten metal hardens. After this, the mold is turned over and the casting is taken out.