(1) Preparation before welding
Use chemical or mechanical methods to strictly clean the surface oxide film on both sides of the weld groove.
Chemical cleaning is to use alkali or acid to clean the surface of the workpiece. This method can not only remove the oxide film, but also remove the oil stain. The specific process is as follows: the volume fraction of 6% to 10% sodium hydroxide solution is soaked at about 70 ℃ for 05min→ Water washing → 15% nitric acid by volume at room temperature for 1 min for neutralization treatment → water washing → warm water washing → drying. The surface of the aluminum alloy after washing is matt silver-white.
Mechanical cleaning can use pneumatic or electric milling cutters, scrapers, files and other tools. For thinner oxide films, 025mm copper wire brushes can also be used to polish and remove oxide films.
Welding should be carried out immediately after cleaning. If it is placed for more than 4 hours, it should be cleaned again.
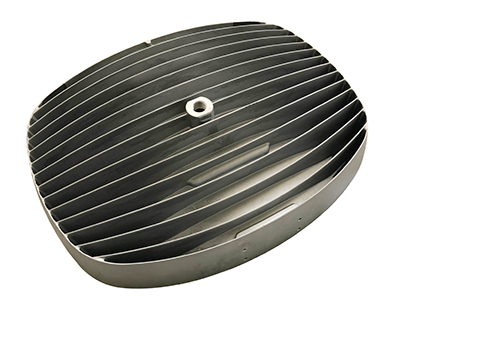
(2) Determine the assembly clearance and tack welding distance
During the welding process, the aluminum plate is thermally expanded, which reduces the gap of the weld groove. If the assembly gap before welding is too small, the grooves of the two plates will overlap during the welding process, increasing the unevenness and deformation of the plate surface after welding. ; On the contrary, if the assembly gap is too large, it will be difficult to apply welding, and there is a possibility of burning through. Appropriate tack welding spacing can ensure the required tack welding gap. Therefore, selecting the appropriate assembly gap and tack welding spacing is an effective measure to reduce deformation. According to experience, the reasonable assembly process parameters for the butt joints with different plate thicknesses are shown in Table 2.
(3) Select welding equipment
At present, there are many types of welding products on the market. Generally, AC tungsten argon arc welding (ie TIG welding) should be used. It is a welding method that uses the arc generated between the tungsten electrode and the workpiece to melt the base metal and fill the welding wire under the protection of argon gas. When the welding machine is working, because the polarity of the alternating current is changing periodically, in each cycle, the half wave is DC positive connection, and the half wave is DC reverse connection. During the positive half-wave period, the tungsten electrode can emit enough electrons without overheating, which is beneficial to the stability of the arc. The oxide film formed on the surface of the workpiece during the reverse half-wave period is easily removed to
Automotive Oil Pan obtain a bright, beautiful and well-formed weld.
(4) Select welding wire
Generally, 301 pure aluminum welding wire and 311 aluminum silicon welding wire are used.
(5) Select welding method and parameters
Generally, the left welding method is used, and the welding torch and the workpiece form an angle of 60°. When the welding thickness is more than 15mm, use the right welding method, and the welding torch and the workpiece form a 90° angle.
When the welding wall thickness is more than 3mm, open V-shaped groove, the included angle is 60°~70°, the gap should not be greater than 1mm, and it is completed by multi-layer welding. When the wall thickness is below 15mm, no grooves, no gaps, and no filler wires are added. When welding fixed pipe butt joints, when the pipe diameter is 200mm and the wall thickness is 6mm, a tungsten electrode with a diameter of 3-4mm should be used, a welding current of 220-240A, a filler wire with a diameter of 4mm, and 1-2 layers of tungsten electrodes should be used. Welded.